1.We use a high-precision flatness tester to place the saw blade on the workbench. The sensor and probe conduct point-by-point scanning to measure the surface undulations with micron-level precision. The flatness error is strictly controlled within ±0.05mm to ensure that the saw blade remains stable and does not deviate during high-speed cutting, resulting in a smooth cut.
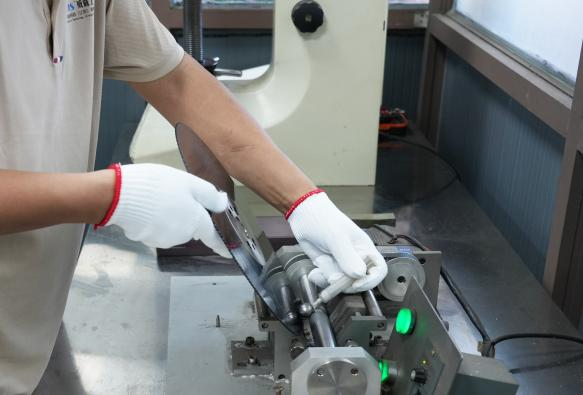
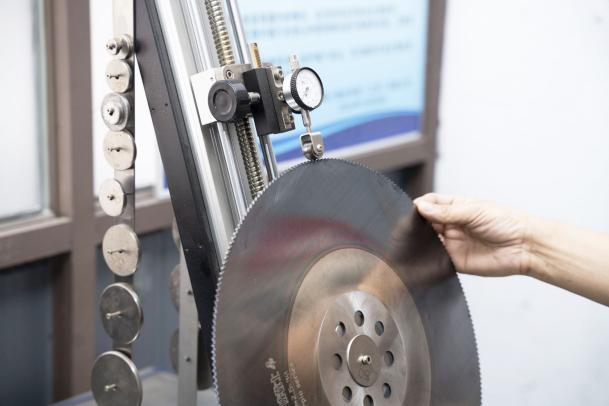
2.brittleness and cracking, while insufficient tension leads to vibration. By strictly controlling the tension, the risk of tooth chipping is reduced, and the safety and efficiency of the operation are improved.
3.Inspection personnel use high-powered microscopes and image acquisition devices to magnify and display the surface details of the saw blades on a computer screen. They carefully search for minor defects such as cracks and pores. Once any abnormalities are detected, immediate corrective actions are taken to ensure that the surface quality of each saw blade meets strict standards, thus providing a guarantee for high-quality cutting operations.
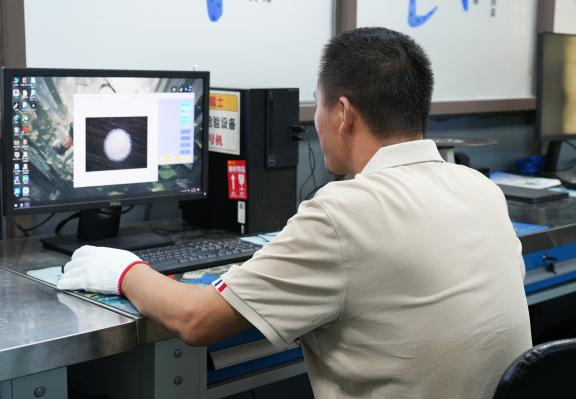
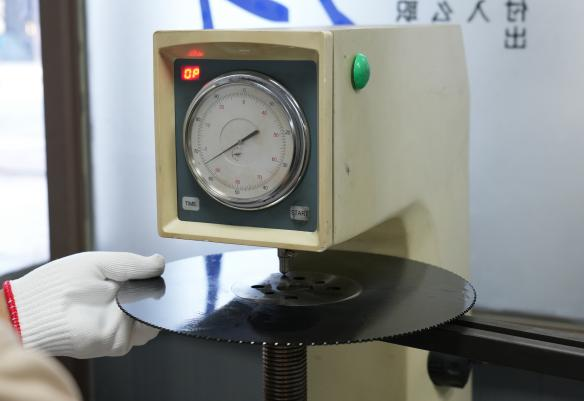
4.We use a Rockwell hardness tester. After fixing the saw blade, a controllable pressure is applied through the indenter, and the hardness value is accurately calculated based on the depth of the indentation. The hardness is strictly required to be maintained within the range of HRC63 - 66, ensuring that the saw blade has both wear resistance and toughness. This helps to enhance the cutting ability, enabling efficient and stable cutting. Every inspection is a guarantee of quality.
5.Inspection personnel use professional equipment to scan the saw teeth through high-precision sensors, and the computer generates images in real time. The system automatically measures parameters such as tooth shape angles and tooth pitches, and quickly compares them with standard data, strictly controlling errors. If the data is abnormal, calibration or rework will be carried out immediately to ensure efficient and stable cutting of the saw blade.
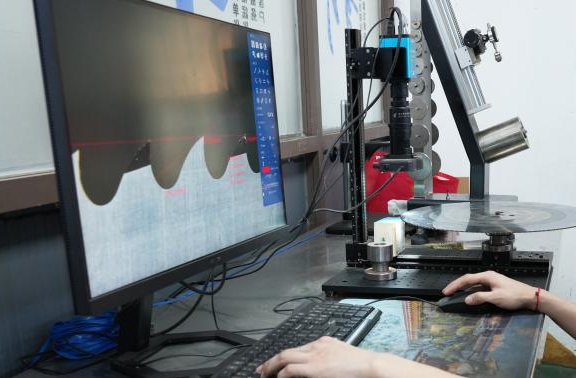
Strict inspection of TCT saw blades
Dimension inspection is critical in the quality control of alloy saw blade production. Staff members meticulously measure the outer diameter, thickness, tooth pitch, and other dimensions of the saw blades according to standards. These dimensions are closely related to cutting performance and precision. Relying on the accuracy of measuring tools and the experience of personnel, each saw blade is ensured to meet dimensional standards, laying a foundation for efficient and stable cutting.
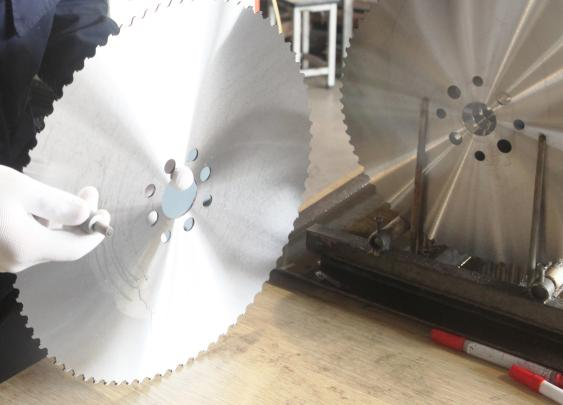
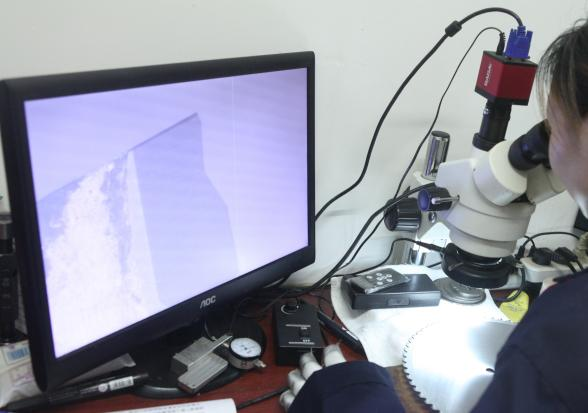
Surface defect inspection is a key link in the quality control of alloy saw blades. Inspectors operate high-power microscopes and image acquisition equipment, fixing the saw blades and magnifying surface details onto a computer screen. With professional experience, they carefully 排查 (inspect for) micro-defects such as cracks and sand holes, immediately recording and addressing any anomalies to ensure the surface quality of each saw blade meets standards. This guarantees the stability of subsequent cutting operations.
Tooth profile inspection is a core process in the quality control of alloy saw blades. Operators fix the saw blades on specialized equipment, and high-precision sensors scan the teeth. Data collected by the equipment is processed by the system to generate visual charts and numerical reports. Inspectors accurately measure and compare parameters such as tooth angle and pitch according to standards and design requirements. When deviations exceed limits, an alarm is triggered, and non-conforming products are promptly handled to ensure the tooth profile accuracy meets the needs of efficient and stable cutting.
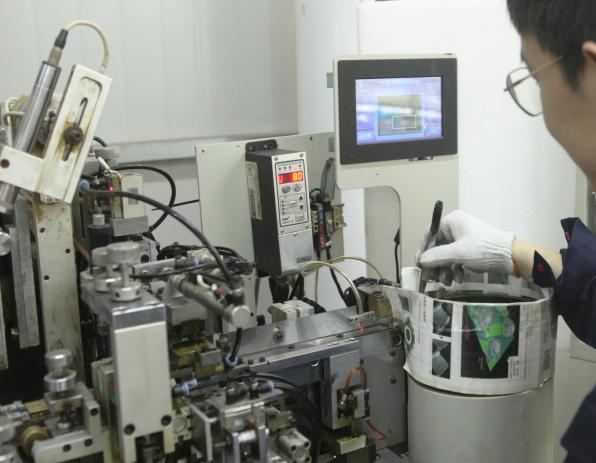